Drive System Test & Modifications
The drive system was not as complex as the lifting mechanism and a decision was made to test it after it had been assembled as part of the prototype. Minimal potential danger was possible to other components when testing the drive system which was a factor in deciding not to test it separately. In addition to this, no components were obstructing the view of the system when in operation and a larger voltage would be required which meant it would be important to view the effects on the shaft supports in the final environment in case the added torque posed any unforeseen issues.
Initially, the drive system was tested after the radio shuttle had been placed at a height in order to prevent the wheels from contacting the ground. If the test was successful, the test would be run again with the radio shuttle on the shelves. The main aim of the drive system test was to view both wheels rotating with the shaft with no belt or pulley drum issues.
​
Both wheels rotated as planned with the shaft at all times, speaking to the successful design of the wheel filler pieces. Moreover, the drive system in general was a success when the voltage supplied was below 12V. Once the voltage increased beyond this point, some minor issues arose with the drive system.
At a higher voltage (which could be required for efficiency purposes when a radio shuttle had a long distance to travel), the belt connecting the two pulley drums was slipping and almost falling completely off the pulley on the drive shaft. The team came to the conclusion that with extended periods of usage, this would almost certainly fall off and render the drive system useless. As the pulley drums were 3D printed and not manufactured in conjunction with the belt originally, the compatibility between the two was perhaps not perfect and resulted in some slip. However, rather than make any adjustments we recommended that the drive system should not be operated at a voltage higher than 12V until either new pulley drums were introduced or a more appropriate belt was introduced to the drive system. No belt issues were noted at a voltage just less than 12V and for the shelves constructed, this produced more than enough speed to cover the distance suitably.
​
​
​
​
​
​
​
​
​
​
​
​
​
​
​
​
Some slip between the pulley drum and drive shaft was noticed especially at a higher voltage. The pulley design included space for a nut and bolt to secure it to the shaft in order for both to rotate with one another. Once this was tightened, negligible slip occurred but employing a similar design as the lifting mechanism with a filler piece and key way would be an overall more secure design. However, the drive system test was conducted again and was deemed acceptable.
​
​
​
​
​
​
​
​
​
​
​
​
​
​
​
​
After certain modifications were made to the model regarding the compatibility with the shelves, the drive system test was again run with the main wheels contacting a surface. Results were similar to the test previously and no further alterations to the design were required.
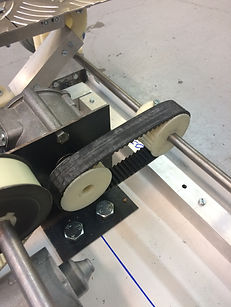
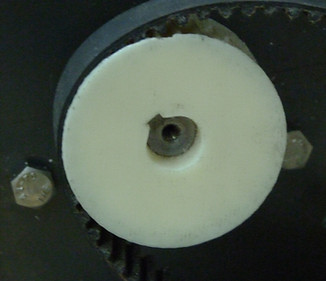